In the vast machinery of industrial and commercial operations, welding machines play an indispensable role. These unassuming devices are the linchpins of modern construction, manufacturing, and repair work, seamlessly melding strength, precision, and innovation into every project they touch. From assembling skyscrapers to maintaining critical pipelines, the industrial and commercial sectors’ reliance on welding machines underscores their fundamental importance.
Page Content
Welding Machines: The Backbone of Industrial Operations
Welding is a process that dates back to ancient times, but its modern incarnation has evolved into a high-tech, precision-driven field. Welding machines are at the core of this evolution, transforming raw materials into robust structures that power industries worldwide.
- The Scale of Dependence
According to a report by Grand View Research, the global welding products market was valued at $16.37 billion in 2022 and is expected to grow at a CAGR of 5.5% from 2023 to 2030. Increased industrial activities, infrastructure development, and the rising demand for automation fuel this surge.
- The Role of Welding Machines
The reliance on welding machines extends across various domains:
Construction: Welding machines are vital for building and bridge structural frameworks.
Automotive: From chassis assembly to exhaust systems, welding ensures durability in vehicle manufacturing.
Energy Sector: In oil and gas, welding machines maintain the integrity of pipelines and rigs. The renewable energy sector also relies on welding for wind turbines and solar panel frames.
Types of Welding Machines and Their Applications
Welding machines come in various types, each catering to specific industrial needs:
- MIG Welding Machines (Metal Inert Gas)
Applications: Automotive, heavy equipment, and sheet metal industries.
Advantages: MIG machines are ideal for high-volume projects because of their speed and ease of use.
- TIG Welding Machines (Tungsten Inert Gas)
Applications: Aerospace, automotive, and artful metalwork.
Advantages: TIG welding provides unmatched precision, making it perfect for intricate projects.
- Stick Welding Equipment
Applications include shipbuilding, construction, and maintenance.
Benefits: The ability to work on painted or corroded surfaces makes stick welders incredibly flexible.
- Welding machines that resist
Applications include the production of electronics and automobiles.
Benefits: For mass manufacturing, resistance welders are economical and effective.
The Effect of Welding Machines on the Economy
Welding equipment are widely used not only for their practical use but also for their role in economic expansion.
- Productivity Boost
Automation in welding, powered by advanced machines, reduces project timelines by as much as 30% (McKinsey & Company). This productivity gain allows industries to meet tight deadlines without compromising quality.
- Cost Efficiency
Modern welding machines minimize material waste and energy consumption. For example, inverter-based welding machines can reduce energy use by up to 30%, making them a sustainable choice for industries prioritizing cost management and environmental impact.
- Job Creation
The global demand for welding machines spurs job creation across engineering, maintenance, and production roles. As the welding market expands, so does the need for skilled labor to operate and maintain these machines.
Technological Advancements in Welding Machines
The welding industry is not static—it evolves alongside technology. Advanced welding machines now integrate features that enhance efficiency and safety.
- Robotics and Automation
Robotic welding systems are becoming standard in high-volume industries. These systems are equipped with sensors and AI, ensure precision and reduce human error. According to Research Nester, robotic welding is expected to grow at a CAGR of 8.5% through 2028.
- Smart Welders
Smart welding machines equipped with IoT connectivity provide real-time data on performance, helping industries optimize operations and reduce downtime.
- Eco-Friendly Innovations
Sustainability is a growing priority. New welding machines are designed with reduced emissions and energy efficiency, aligning with global green initiatives.
Challenges in Industrial Reliance on Welding Machines
While welding machines are indispensable, challenges persist:
- Skilled Labor Shortage
Despite their advanced features, welding machines require skilled operators. A report by the American Welding Society projects a shortage of 375,000 welders in the U.S. alone by 2026.
- High Initial Investment
Modern welding machines come with a premium price tag, which can be prohibitive for small and medium enterprises (SMEs).
- Maintenance and Downtime
Regular maintenance is essential to prevent operational disruptions. Downtime due to machine failure can result in significant financial losses.
Future Outlook: Welding Machines as Industry Catalysts
The reliance on welding machines will deepen as industries embrace advanced manufacturing techniques. Key trends shaping their future include:
Adoption of Additive Manufacturing: Welding machines are now integral to 3D printing technologies, particularly in metal fabrication.
Expansion into Emerging Markets: Developing countries invest heavily in infrastructure, driving demand for welding machines.
Enhanced Training Programs: To address the labor shortage, industries partner with educational institutions to train the next generation of welders.
Conclusion
The industrial and commercial sectors’ reliance on welding machines is a testament to their versatility and indispensability. These machines are more than just tools—they are the backbone of modern industry, enabling everything from skyscrapers to renewable energy solutions.
As technology advances and industries evolve, welding machines will continue to adapt, pushing the boundaries of what’s possible. For industries striving for efficiency, precision, and sustainability, the welding machine is not just a necessity—it’s a game-changer.
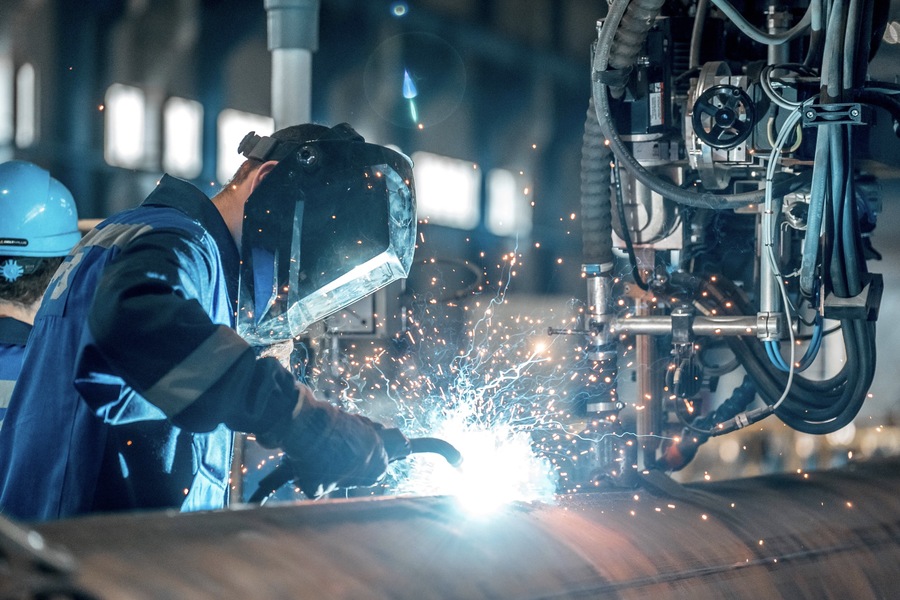